Interview: Hochleistungsbatterien - Entscheidend für E-Mobilität der Bahnen
Akkumulatoren sind ein zentrales Element für die Zukunft der Schienenfahrzeuge im Bereich E-Mobilität. Über aktuelle Forschungen unterhielt sich Bahn Manager mit einem der führenden deutschen Experten Dr. Andreas Würsig vom Fraunhofer-Institut für Siliziumtechnologie (ISIT) in Itzehoe.
bahn manager Magazin: Herr Dr. Würsig, in Schienenfahrzeugen brauchen wir große Batterien, weil die Fahrzeuge schwer sind. Es scheint, Sie machen sich in Ihren Forschungen an Anode und Kathode gleichzeitig heran, während sonst die meisten nur an die Anode herangehen, andere nur an die Kathode. Sie haben auch einen Lithium- Booster entwickelt. In welche Richtung gehen aktuell Ihre Forschungen?
Dr. Andreas Würsig: Wir beschäftigen uns derzeit mit verschiedensten Projekten, wobei ein spezieller Focus auf der Entwicklung auf Batteriezellen und Batteriesysteme mit hoher Leistungsfähigkeit liegt. Hochenergiebatterien, also Batterien zum Beispiel mit einer besonders hohen Reichweite für die Elektromobilität, besitzen üblicherweise nur eine begrenzte Leistungsdichte und umgekehrt. Unser Ziel ist es, unter anderem für Anwendungsgebiete wie die Elektromobilität, aber auch zur Zwischenspeicherung Erneuerbarer Energien Akkumulatoren zu entwickeln, die sich besonders schnell laden und entladen lassen. Das Besondere an unserer Technologie sind zum einen die Materialien, die wir verwenden, die neben einer hohen Leistungsdichte eine besonders hohe Zyklenstabilität aufweisen. Hochleistungsbatterien werden ja deutlich öfter zyklisch geladen und entladen als Hochenergiebatterien. Wir haben eine Batterie entwickelt, die man mit über 15.000 Zyklen belasten kann, laden und entladen, ohne dass sie wesentlich an Kapazität verliert, und darüber hinaus bietet diese Technologie eine sehr hohe Eigensicherheit, was für viele Anwendungsszenarien wesentlich ist. Das bedeutet, dass sich in einem Schadensfall die Gefahr eines Brandes deutlich vermindert.
Im Bereich Anode – Kathode sind bisher offenbar noch nicht alle Varianten durchgetestet. In welche Richtung geht das jetzt bei Ihnen, Sie testen auch spezielle Legierungen? Das scheint bei Ihnen einige Schritte weiter zu gehen, Sie testen auch die Möglichkeiten deutlich tiefer, als man das von den schon in der Anwendung befindlichen Modellen kennt?
Es gibt, wie Sie richtig gesagt haben, eine ganze Bandbreite von verschiedenen Materialien sowohl auf der Anoden- als auf der Kathodenseite, und man sucht sich sozusagen in einem Baukasten die für eine bestimmte Anwendung geeignetsten Materialien aus und muss diese dann natürlich noch gut aufeinander abstimmen. Das dafür notwendige Knowhow ist wesentlich für eine zügige Entwicklung neuer Batteriezellen und wurde an unserem Institut über viele Jahre aufgebaut. Für Hochleistungsbatterien verwenden wir beispielsweise das sogenannte Lithium-Titanat. Dieses Material zeichnet sich unter anderem dadurch aus, dass es besonders schnell geladen und entladen werden kann. Dieses kombinieren wir dann mit einem ähnlich schnellen Kathodenmaterial. Oft sind verschiedene Materialkombinationen möglich, die sich aber in Aspekten wie Leistungsdichte, Langzeitstabilität und Energiedichte, aber auch in den Kosten unterscheiden. Die Materialien werden dann zunächst in Zellprototypen geprüft, die wir auch in Kleinserie aufbauen können, und auf Basis der Messdaten und unter Beachtung der jeweiligen Anwendung wird über die finale Lösung entschieden. In mehr und mehr Projekten werden Zellen bei uns auch in Systeme integriert. Das heißt, unsere Forschung und Entwicklung endet heutzutage nicht mehr bei der Zelle, sondern wir betrachten auch das Gesamtsystem und sind daher in der Lage, Zelle und System optimal aufeinander abzustimmen. Dabei entwickeln wir auch die Zellelektronik inclusive des Batteriemanagementsystems selbst und können diese auf die gewählte Materialkombination abstimmen. Je nach Anwendung wird dann das geeignetste Material ausgewählt.
Von der Anzahl der Ladezyklen her und zeitlich gesehen, nach wie viel Jahren Einsatz ist eine solche Batterie dann an der Grenze der Nutzbarkeit?
Es gibt tatsächlich zwei verschiedene Alterungsprozesse bei Lithium-Batterien, die durch zum Teil unterschiedliche chemische und physikalische Prozesse hervorgerufen werden. Die Alterung ist zum Einen davon abhängig, wie oft eine Zelle geladen und entladen wurde. Es gibt jedoch auch eine kalendarische Alterung, die die Lebensdauer der Batterie auch dann begrenzt, wenn sie nicht genutzt wird. Für die Batterie-Chemien für Hochleistungsspeicher, mit denen wir uns aktuell beschäftigen, gehen wir von einer Lebensdauer von über 20 Jahren aus. Das ist zunächst natürlich nur eine Prognose, die darauf beruht, dass die Batterien unter erhöhten Temperaturen getestet werden. Aus den Messergebnissen wird dann sozusagen in die Zukunft gerechnet. Ob dies dann tatsächlich so eintritt, kann man natürlich erst im Realbetrieb erleben. Ansonsten liegt die Lebensdauer heutiger Batterien im Automobilbereich mittlerweile bei über 10 Jahren. Hier wurden in den letzten Jahren schon große Fortschritte erzielt. Wir hoffen natürlich, dass unsere Forschung dazu beiträgt, diese Nutzungszeit noch deutlich zu erhöhen.
Das wäre fabelhaft. Bezogen auf die in Pkws bisher eingesetzten Batterien scheint schon durch den Energieaufwand bei der Herstellung ein Einsatz über sieben Jahre nötig zu sein, um dort in der Energiebilanz zur Null zu kommen. Danach beginnt erst der volle energetisch-umweltpolitische Nutzeffekt. Können Sie bestätigen, dass der Aufwand auf der Energieseite von der Herstellung her sehr hoch ist?
Der energetische Aufwand für die Zellfertigung ist tatsächlich nicht unerheblich. Insbesondere im Bereich der Elektrodenfertigung, aber auch in der Formierung, also während des erstmaligen Zyklens der Batterien, sind erhebliche Energiemengen einzusetzen. Das bedeutet für uns letztlich, dass eine Batterie- Zellfertigung nur dann nachhaltig ist, wenn sie mit 100 Prozent erneuerbaren Energien betrieben werden kann.
Das andere, was in Zügen noch eine Belastung ist, ist die Frage des Gewichtes. Als Richtschnur scheint zu gelten, eine Tonne Batteriegewicht reicht für 10 Kilometer Zugfahrt. Dann ist es kein Wunder, dass alle Zughersteller auf der letzten InnoTrans erklärt haben, dass sie mit einer Batteriefüllung 70 bis 80 Kilometer Strecke befahren können. Das reicht aber nicht immer aus, wenn ich überlege, wie viel soll der Zug in einem Tagesfahrplan fahren. Lässt sich die Gewichtfrage noch etwas optimieren?
Da sprechen Sie das Thema Energiedichte an. Daran wird im Moment sehr intensiv gearbeitet, werden neue Konzepte und auch neue Materialien untersucht. Um einen Vergleich zu bringen, die heutigen Energiedichten bezogen auf das Gewicht bewegen sich aktuell um die 260 bis 280 Wattstunden pro Kilogramm. Da ist sicherlich noch ein bisschen Luft für die konventionelle Lithium- Batterietechnologie drin, aber dann kommt man irgendwo an physikalische Grenzen. Es gibt aber neue Batteriekonzepte wie beispielsweise die Lithium-Schwefel-Batterie, an der bereits seit längerem intensiv geforscht wird und mit der bereits Energiedichten von über 500 Wattstunden pro Kilogramm demonstriert worden. Das ist ein Batteriekonzept, das man sich durchaus in der Anwendung für eine Lokomotive vorstellen könnte, da hier das Gewicht oft wichtiger ist als das Volumen. Im Automotiv-Bereich ist man da aktuell skeptisch, weil die volumetrische Energiedichte, also die Energie bezogen auf das Gesamtvolumen dieses Batteriekonzeptes, nicht so viel besser ist als bei heutigen konventionellen Lithium-Batterien. Jedoch bedarf es für die Lithium- Schwefel-Batterie sicher noch einiger Jahre Forschung. Ein Problem ist zum Beispiel ihre bislang ungenügende Langzeitstabilität.
Für Busse oder eben Züge, bei denen Gewicht und Reichweite Entscheidungsfaktoren sind, ob das Fahrzeug angeschafft wird, kann man also sagen, die Forschung ist noch lange nicht am Ende, sie beginnt eigentlich jetzt erst richtig? Haben Sie einen Stab von Leuten für Brainstorming und Evaluation?
Also, ich sehe durchaus noch einiges an Luft in der Batterietechnologie. Die Lithium-Batterie ist noch eine relativ junge Technologie. Die gibt es jetzt erst seit etwa 30 Jahren in den ersten Konzepten. Wir haben tatsächlich einen Stab von Wissenschaftlern an unserem Institut, die auch Publikationen auswerten. Auch aus Gesprächen mit anderen Instituten, mit anderen Forschungseinrichtungen kommt man auf neue Ideen, die man dann versucht, im eigenen Arbeitskreis umzusetzen.
Sehen Sie eine Chance für Deutschland, auch als Produzent in Erscheinung zu treten? Das ist ja ein bisschen peinlich, wenn das wichtiger werden soll für uns, und wir müssen die Batterien dann immer in Übersee anschaffen.
Da sprechen Sie ein sehr wichtiges Thema an. Es ist tatsächlich so, dass die Batteriezell- Fertigung in Deutschland nur in einem sehr geringen Maßstab stattfindet und die Bundesregierung aktuell große Anstrengungen unternimmt, um mittels geeigneter Förderung auch in Deutschland eine international konkurrenzfähige Batteriezellfertigung zu etablieren. Es ist letztlich eine Schlüsseltechnologie für die Energiewende und die Elektromobilität. Auch große Automobilproduzenten haben das erkannt und investieren mittlerweile erhebliche Summen in eine eigene Zellfertigung oder beteiligen sich am Aufbau entsprechender Unternehmen. Eine Chance sehe ich auf jeden Fall, aber es muss bald reagiert werden, weil der Vorsprung gerade im asiatischen Bereich natürlich schon groß ist. Wir haben hier in Deutschland eine vielfältige Forschungslandschaft, die in den letzten Jahren aufgebaut wurde, das heißt, rein technologisch können wir auf jeden Fall mithalten. Jetzt geht es darum, das wirklich in eine großvolumige Fertigung zu übersetzen.
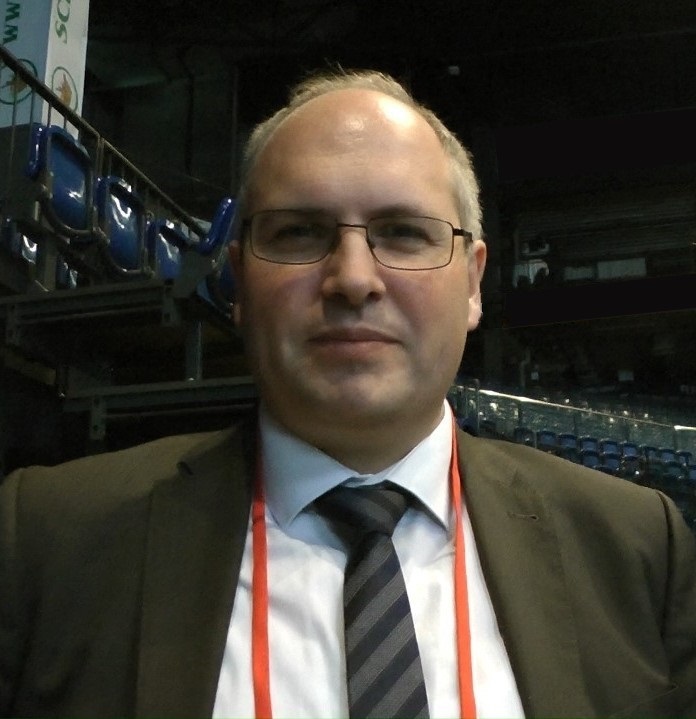
DR. ANDREAS WÜRSIG
Würsig promovierte nach Abschluss des Chemiestudiums an der TU in Freiberg am Paul Scherrer Institut der ETH Zürich. Seit mehr als 15 Jahren mit der Entwicklung fortschrittlicher Lithium-Ionen-Batterien beschäftigt, Inhaber mehrerer Patente. Seit 2017 stellvertretender Leiter des Geschäftsfeldes „Leistungselektronik“ und Leiter der Gruppe „Batteriesysteme für spezielle Anwendungen“ am Fraunhofer-Institut für Siliziumtechnologie (ISIT) in Itzehoe.